The ERP system (Enterprise Resource Planning) is an integrated enterprise management information system in the modern sense. It provides automation of planning, accounting, control and analysis of all business processes. The ERP system is based on the management of a data warehouse, which contains all the necessary corporate information: financial, production, personnel, inventory information, etc.
ERP systems
The ERP system consists of a set of various software modules that support automation of subject areas of activity. Each module of the ERP system is focused on solving a specific group of tasks: production planning, procurement management, inventory control, personnel management, marketing, sales management, etc. Modern ERP systems can be implemented at almost any enterprise, any field of activity and any scale.
ERP systems development
ERP systems are the development of enterprise management systems that originated in the mid-60s. APICS (American Production and Inventory Control Society) formulated the basic principles of the enterprise inventory management during this period. These principles formed the basis of the MRP (Material Requirement Planning) concept. The first MRP systems were developed based on this concept. They were intended for manufacturing enterprises with a discrete type of production. MRP systems provided optimization of the company's inventory management based on the production plan.
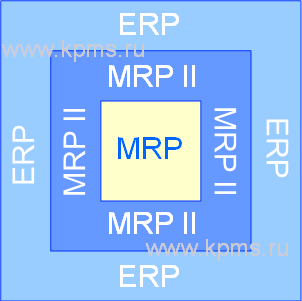
A further development of the MRP concept was the MRP II (Manufacturing Resource Planning) concept, which appeared in the late 70s. The systems built on the basis of this concept provided forecasting, planning and control of production throughout the entire cycle: starting from the purchase of raw materials and ending with the shipment of goods to the consumer. This type of systems (MRP II systems) is focused on the effective planning of all resources of the production enterprise, including the financial component.
ERP systems appeared in the late 80s as a result of the evolutionary development of MRP II systems and the growth of computing and information technology facilities. These systems have further expanded the field of enterprise management based on process automation. They integrated both internal and external information necessary for the work of the organization. It have been added the functions of human resource management, finance, sales, marketing, service, etc.
MRP:
- product specification management;
- inventory management;
- production order management;
- preparation of the production schedule;
- production control and management;
- managing material needs.
MRP II:
- all MRP functions;
- financial management;
- business planning;
- resource planning;
- production planning;
- sales planning;
- managing customer orders;
- development of the main production plan;
- volumetric production planning.
ERP:
- all MRP II functions;
- financial planning and modeling;
- business planning and modeling;
- sales planning and management;
- marketing planning and management;
- sales planning and management;
- resource management and needs modeling;
- production management and production modeling;
- supply management.
ERP system structure
Usually, ERP systems consist of various modules that implement the organizations needs in process automation. Each of the modules is focused on a specific area of activity or business process. ERP systems contain elements of MRP and MRP II systems because it appeared as a result of the evolutionary development of these systems.
The structure of the ERP system can be divided into two components according to the composition of the used modules: basic elements and extended elements.
The basic elements include all the system functions that carry out production management: enlarged and detailed capacity planning, development of the main production plan, planning of material requirements, processing of product specifications, production routing, procurement and inventory management. These elements can be implemented in one or more ERP system modules (depending on the developer).
Extended elements include all the functions that ensure the production operation. These elements are implemented as separate modules as a rule.
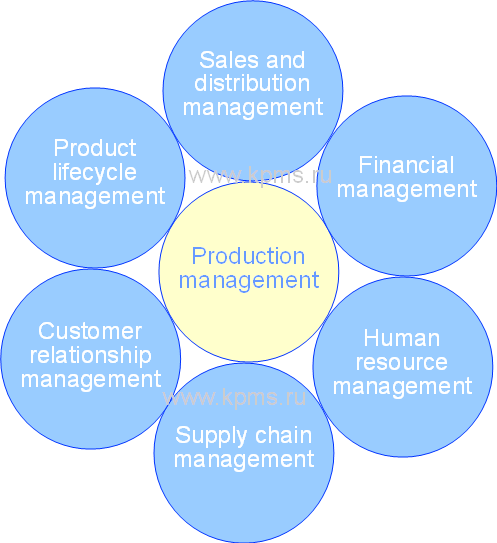
Such elements include:
- financial management. This element of the ERP system allows you to maintain the general ledger, manage settlements with debtors and creditors, perform accounting of fixed assets, manage cash, plan financial activities, keep financial statements and accounting, etc.
- human resource management. It allows you to carry out personnel accounting, perform payroll accounting, keep records of working hours, work schedules, plan personnel, manage staff motivation.
- supply chain management. This element is one of the key elements in the ERP system. It allows you to predict demand, plan and manage logistics both inside the enterprise (warehouse and production logistics) and outside it (logistics of external supplies and sales of finished products), manage purchases and suppliers.
- customers relationship management. This element of the ERP system performs the same functions as individual CRM systems. The functionality of this module largely depends on the manufacturer, but the main actions include sales management, accounting for customer interaction, marketing management.
- product lifecycle management. It allows you to manage the life cycle of a product from its development to disposal. The ERP system modules make it possible to manage product data, control design, manage the life cycle of equipment, and manage customer needs.
- sales and delivery management. This ERP system module allows you to plan and manage sales channels, manage orders, manage pricing, and manage transport.
The composition of elements and modules may vary depending on the manufacturer of the ERP system. For example, some manufacturers offer quality management modules, project management modules, environmental management modules, etc. Modern ERP systems allow you to implement both full functionality and individual modules.
ERP system advantages and disadvantages
The use of ERP systems significantly improves the quality of organization management. They simplify control over the workflow between departments, reduce the costs associated with duplication of information and tasks, and reduce the costs arising from the operation of disparate management systems.
The use of a full-fledged ERP system gives the organization the following advantages:
- processes control. ERP systems make it possible to exercise control over all important processes of the organization. Control can be based according to a hierarchical system: from the operational level to the level of strategic management.
- synchronization of processes. All the processes of the organization can be organized in the form of a consistent and interrelated workflow transferred from department to department. Workflows can be synchronized due to the use of an ERP system. This guarantees the efficient execution of processes that are closed to individual departments, but affect the processes common to several departments.
- reporting standardization. ERP system reporting tools unify all types of reports and statistical data required for management. These reports can be created for all processes, departments or functions in real time.
- information systems unification. There is no need to support disparate management information systems because the ERP system is implemented in all departments of the organization (when implementing all the functionality of the ERP system). All functions of individual systems can be integrated into an ERP system.
- management functions expansion. Most ERP systems allow the use of corporate knowledge management modules. This enables the organization to significantly expand its management functions by creating a corporate knowledge base.
- integration with suppliers/customers. Many modern ERP systems allow suppliers/customers to perform part of the organization's functions (order formation and tracking, inventory control and replenishment, etc.).
- adaptation to business needs. ERP systems have various modules that can work both in relation to the basic functions, and separately from them. The composition of the tasks in each module is customized to the needs of the organization.
- data centralization. The principle of operation of the ERP system implies the creation of a single database that store all management information. The data is stored centrally, which provides quick access to the necessary information, reliable protection and archiving.
- data protection. Its own security policies can be created for each group of users in the ERP system, which provides more reliable data protection. The work of each user can be monitored. All operations and actions performed by the user can be controlled at the expense of the ERP system.
- interaction improved. ERP systems provide "transparency" the work results of each department. This makes it possible to establish horizontal links between departments and improve their interaction.
- integration with low-level control systems. ERP systems provide communication with low-level control systems (machines, production complexes and other equipment) due to the use of the API interface.
- control of interrelated activities. ERP systems facilitate the tracking of orders, inventory, revenue, sales and all related activities due to the availability of various modules.
- scaling. ERP systems allow you to scale solutions for large companies with a distributed structure and geographically remote divisions. This makes it possible for geographically remote units to have a unified management system.
ERP system cannot fully meet all the needs of an organization like any other management system. The ERP system has limitations and disadvantages. These disadvantages may be related both to the functionality of the system and to the conditions of its acquisition, implementation, use and support.
The disadvantages of an ERP system include:
- high cost. A full-fledged ERP system is quite expensive for any organization. The cost of an ERP system includes many components. The main of its are: the cost of software and hardware, the cost of planning, implementation, configuration and testing, the cost of maintenance.
- the long time of implementation. The implementation of a full-fledged ERP system can take from 1 to 3 years for large organizations. The organization's processes may be unstable during this period.
- the level of compatibility with business processes. Systems with a small number of settings will not correspond to real business processes. There is a problem of modernization when changing processes for systems that have a lot of settings.
- difficulties of mastering. ERP systems have complex user interfaces as a rule. Long-term training of users is necessary for the successful implementation and operation of an ERP system.
- additional indirect costs. The enterprise may need to update some of the equipment, software, communication channels for the implementation of the ERP system and its normal operation.
- data transfer. The ERP system replaces the existing disparate management information systems. The data stored in these systems cannot always be easily integrated into the ERP system database. Data transfer may be difficult or even impossible.
- dependence on the supplier. The acquisition and implementation of an ERP system is a costly process. The company is forced to use services of one supplier in order to maintain the system and update it.
ERP system choosing criteria
There are a large number of ERP system offerings on the market. Suppliers offer both ready-made solutions (ERP systems of large manufacturers) and custom developments. ERP systems can be based on "cloud" services, object-oriented architecture or "client-server" applications depending on the implementation technology. Choosing a system and its supplier becomes a difficult task.
The selection criteria can be divided into several groups in order to determine which ERP system is most suitable for an organization.
Common groups of criteria are:
- the organization needs. This group of criteria is related to the current and future needs of the organization, its size, working conditions and market requirements.
- applied technologies. This group includes criteria related to the technology of the ERP system and the methods of implementation.
- functionality. This group defines a set of criteria for the composition of tasks and modules of the ERP system necessary to meet the needs of the organization.
- support. The set of criteria of this group determines the conditions of technical, information and service support of the ERP system from the supplier (vendor).
- cost of ownership. This group of criteria includes all criteria related to the acquisition and operation of an ERP system.
The group of criteria "organization needs" may include:
- compliance with the organization business processes. The ERP system should be able to be configured for the organization's processes. This criterion determines the flexibility of the system in case of changes in the company's activities.
- scalability. The ERP system should allow you to replicate solutions for several divisions or several types of company activities. Also, it should be able to adapt to the scale of the organization.
- compliance with the organization's strategy. The ERP system is operated for a long period of time. It should help to implement the company's strategic plans. The choice of the system should be carried out taking into account the prospects for development.
- availability of industry solutions. The organization's processes depend on the industry and the market in which it operates. These factors must be taken into account when choosing a system.
The group of criteria "applied technologies" may include:
- software architecture. It is necessary to choose the appropriate software architecture of the ERP system depending on the needs and capabilities of the organization (for example, "cloud services", "client-server" architecture or "object-oriented" architecture).
- technical architecture. This selection criterion is interrelated with the previous one. The choice of technical architecture may require the organization to update communication channels, hardware, and computer equipment.
- ERP system implementation technology. This criterion depends on the service provider. Large manufacturers of ERP systems offer to apply the technology of implementation for their software product as a rule. SAP, ORACLE, Microsoft, etc. have such technologies.
The group of criteria "functionality" may include:
- the composition of the modules. The choice of ERP system modules should be carried out depending on the current and future needs of the organization. The system should be able to expand in functionality.
- integration. It is necessary to take into account the possibility of integration with existing management systems in interrelated areas when choosing a system.
- visibility. An essential element of the ERP system functionality is the simplicity of the interface and the usability. It is necessary to take into account the possibility of interface configuration to meet the needs of users.
- compliance with the regulatory framework. The ERP system affects many areas of the company's activities that are regulated by law. An important selection criterion will be the ability of the system to adjust to the requirements of local legislation.
The group of criteria "support" may include:
- support cycle. It is necessary to determine how long the supplier will support the system when choosing an ERP system. Is there a possibility of switching to a new version of the ERP system? Is there a possibility of updating the system for the requests of the organization?
- availability of a support service. Users of the ERP system will always have questions and difficulties in the work. It is important that the supplier can guarantee the support of the system users for the effective operation of the system.
- implementation experience. This criterion is related to the work of the ERP system provider. It is necessary to pay attention to the number of successful implementations of ERP systems from a particular supplier.
The group of criteria "cost of ownership" may include:
- the cost of the software. It is necessary to purchase licenses for use an ERP system. You need to take into account the method of calculating the cost of these licenses (for example, for a group of users or for one workplace, etc.).
- the cost of hardware. The cost of hardware may vary significantly depending on the used architecture. The organization may need to purchase server equipment, update the fleet of computing facilities.
- the cost of maintenance. This criterion is also significant as part of the costs of purchasing an ERP system.
- the cost of upgrading and updating. The cost of updates and upgrades may equal or exceed the cost of the initial purchase for some ERP system vendors.
ERP system implementation
The implementation of an ERP system is usually a long and complex process. Each major ERP system manufacturer has developed its own technologies and implementation methods. These techniques are somewhat different from each other, but the general procedure is basically the same. The procedure for implementing an ERP system may vary depending on the software and hardware architecture of the ERP system. These techniques have a value when choosing a service provider.
The organization needs to take a number of actions for the successful implementation of the implementation project.
Such actions include:
1. Preparation of implementation. It is necessary to determine the main goals for which the ERP system will be implemented. This will allow you to clearly understand the results and expectations from the implementation of the ERP system. It is necessary to assess the budget that the organization will be able to allocate for implementation, because the implementation of an ERP system is a rather expensive project. The person responsible for the project is determined, and key specialists (project team members from the organization) are identified, the order of their interaction is determined at this stage.
2. Business analysis. These actions are the most critical in the entire project. As a rule, an ERP system should work for a decade or more. Therefore, it is necessary to determine the prospects for the development of both the organization itself and the market for a long period.
The organization should evaluate at this stage:
- prospects for the development of the market and the company for several years;
- composition and possibility of business processes development of the organization;
- automation needs.
3. Choosing an ERP system. The choice of the system should be based on the current and future needs of the business. It is necessary to be guided by the criteria specified above when evaluating various options (criteria for choosing ERP systems). It is advisable to select at least 3 variants of systems from different manufacturers in order to choose the system most suitable for the needs of the business.
4. Choosing a supplier. As a rule, there are many suppliers of the same ERP system on the market. These are vendors or system integrators. They offer a range of services for the technical implementation of the ERP system. It is necessary to pay attention to supplier specialization when choosing an ERP system. There are three types of supplier specialization.
Each of the supplier types has its advantages and disadvantages:
- horizontal specialization. Such companies have a large number of customers who work in different industries. As a rule, such suppliers have advanced support services. They have "typical" approach to implementation ERP system for all customers.
- vertical specialization. These suppliers specialize in working with customers from a limited number of industries (from one to three). This allows them to create solutions specifically tuned to the specifics of the industry. The approach to implementation of such companies is "sharpened" for a specific industry.
- client-oriented specialization. These suppliers implement an ERP system to the customer needs. They take as a framework the basic functionality of the ERP system and refine it to the customer's business conditions. This option has a significant disadvantage associated with updating the system and the stability of its operation.
5. Project management. The person responsible for the implementation of the ERP system and the specialists of the organization should manage the project within the company. They must maintain a project plan, monitor deadlines, budget, scope of work, compliance with implementation goals. Another important task of project management is to coordinate the interaction of the organization's employees with the supplier's representatives (the implementation team from the supplier).
6. Testing. There is a risk of errors in the operation of the system even with the best implementation. It is necessary to provide mandatory testing of the processes, departments and modules of the ERP system during the commissioning of the ERP system functionality. The best way to test is to perform parallel work in the old system and in the implemented ERP system. This will get remove of the main errors.
7. Trainings and learning. Employee training is a prerequisite for the operation of the ERP system. It may take several weeks depending on the complexity of the system. You need to make sure that the ERP system has been tested before starting the training. One of the bad options is when the service provider combines testing and user training. Employees of the organization (future users of the system) act as system testers in this variant.
8. Commissioning. Commissioning is an important point in the process of implementing an ERP system. There are two options for putting the system into operation: launching the system immediately throughout the organization, and phased commissioning. The second option is more preferable, because it allows you to gradually switch to new working conditions. Only part of the business (individual processes or departments) will be affected in case of errors or problems in the work, and not the entire organization.
The main errors in the ERP system implementation
The implementation of an ERP system is one of the most difficult, time-consuming and expensive tasks for improving activities. Problems and errors always arise during the implementation, to one degree or another affecting the timing, cost, and effectiveness of the project.
The main mistakes of the ERP system implementation project include:
- poor planning. The implementation of the ERP system must be carefully planned for the successful of the project. Poor planning often leads to a loss of priorities, confusion with process automation, poor understanding of the current and future state of processes.
- poor evaluation of ERP system suppliers. Organizations are poorly considering the issue of choosing ERP system suppliers. As a result, the choice is made in favor of suppliers who have offered the minimum price. Often, the supplier reduces the price in order to get at least one client and work out the implementation of a new system for himself. It may turn out that the functionality of the ERP system is severely limited or the system works with errors after the completion of the project.
- lack of needs understanding. Many organizations do not understand what functions and modules they need, what the organization needs can be automated through an ERP system. This leads to the fact that a lot of unnecessary and unused functions and modules are being implemented, or the necessary functions are used only in a limited way.
- insufficient understanding of time and resource costs. As a rule, organizations underestimate the time and resources required to implement an ERP system. This leads to excessive expectations from the system. Employees of the organization begin to believe that the ERP system will start working in full in a short time and it will not take much effort to work.
- lack of qualified personnel in the implementation team. A common mistake of ERP system implementation projects is to involve simple performers in the project team. The project team should include highly qualified specialists (key employees) in each area of the organization's activities: finance, management, procurement, production, warehouse, etc.
- poor of priorities. Organizations do not set a priority in achieving goals before starting a project. This leads to the fact that during the implementation of the ERP system, many tasks have to be solved, constantly switching between them. The implementation time increases and additional errors and problems appear as a result.
- employees are not trained. Insufficient or complete lack of employee training is a common reason for the unsuccessful implementation of an ERP system. Employees do not understand how to work in the system and this causes rejection. The system will be unclaimed and its functionality will be used to a limited extent.
- underestimating the accuracy of the data. The ERP system is based on data processing. The accuracy and efficiency of the system will depend on the reliability and accuracy of the data that is entered into the ERP system. It is necessary to initially enter reliable and accurate data into the system to reduce errors. Employees working with the system should carefully check the data before entering into the system.
- using outdated applications. Another problem that leads to low efficiency of ERP system implementation is the continued use of outdated applications. The work is duplicated in the ERP system and old applications. Organizations continue to use them because their support and license renewal have been paid for. This leads to the fact that the transition to work in the ERP system is delayed.
- effective system testing is not carried out. ERP system vendors offer to conduct testing on a limited number of users. Such testing will not be able to identify all disadvantages and will not allow you to simulate a real user load.
- lack of a maintenance and modernization strategy. It will quickly become obsolete if the company does not develop a strategy for the maintenance and modernization of its ERP system. The technical (hardware) part of the ERP system requires modernization, because the amount of data grows over time, and new computing power is required. The software part must be constantly upgraded in accordance with the changing requirements of legislation and the market.
The above implementation problems are the most common. There are always problems specific to each enterprise or organization. An effective method to avoid or minimize losses from such errors is careful preparation and planning of each stage of the ERP system implementation project.