Six sigma is a popular management concept aimed at improving the quality of an organization's work. This concept was developed in the 1980s by Motorola in order to reduce deviations in the production processes of electronic components. It was based on statistical methods of process management, and the work of a Japanese quality specialist - Genichi Taguchi.
Six sigma
6 sigma is considered both as a philosophy, as a methodology, and as a set of tools for improving work in the modern insight. It is used in organizations of various fields of activity – industrial enterprises, medical institutions, banks, multinational corporations, etc.
The term 6 sigma, which is used in the name of the concept, means the standard deviation of a random variable from the average value. This term is used in mathematical statistics. A random variable can be described by two parameters - the average value (denoted by the symbol mu) and the standard deviation (denoted by the symbol sigma).
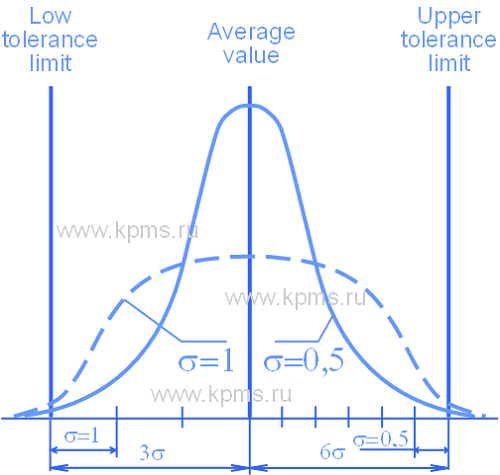
It is possible to estimate the probable proportion of process defects when using the average value and standard deviation. In this case the process quality parameter is considered as a random variable. Preliminary, it is necessary to set the upper and lower limits of the tolerance field of the quality parameter. If the tolerance field will be the more then the proportion of usable products of this process will be the greater. If the sigma value will be more then the proportion of usable products will be the smaller.
It is necessary to reduce the sigma value for a given tolerance field in order to increase the proportion of suitable products, thereby increasing the number of them that fit into the tolerance field.
The number of defective products of the process can be 3.4 (three whole and four tenths) per one million in the variant where six sigma values hold from the average value to the nearest limit of the tolerance field. The possible number of defective products of the process is 66807 per one million in the variant where three sigma values hold.
The essence of the six sigma concept is to achieve a reduction in the value of the standard deviation for a given tolerance field by using various methods and process management tools.
6 sigma as a philosophy
The Six Sigma philosophy is based on an approach of continuous improvement of processes and reduction of the number of defects. The continuous improvement approach should be implemented in the organization. The improvement can be achieved through radical changes (process reengineering approach) or through minor permanent improvements (kaizen approach). The purpose of improvements may be to improve product safety, improve quality, shorten the production cycle, improve jobs, reduce costs, etc.
The key elements of the 6 sigma philosophy are:
- customer satisfaction. Customers determine the quality level of work. They expect high quality products, reliability, adequate price, timely delivery, well service, etc. Quality requirements are hidden in each element of customer expectations. The organization must identify and satisfy all these requirements.
- processes definition, indicators of process and methods of process management. It is necessary to look at the processes from the customer's point of view in order to improve the quality of work. It must be eliminated all processes elements that do not make value to the customer.
- teamwork and staff involvement. The results of an organization's work are the labor of its employees. Each employee must be interested in work and high results in order to achieve high quality. Employee engagement leads to customer satisfaction increased.
6 sigma as a toolkit
6 sigma uses a set of various quality tools in order to carry out improvements, enhancement, and process management. Process management can be carried out on the basis of qualitative and quantitative indicators. Each organization can use its own set of tools. Examples of such tools are - statistical process management based on Control charts, FMEA analysis, Pareto diagram, Ishikawa diagram, Tree diagram, etc.
The Six Sigma toolkit has expanded through the application of this concept in many areas of activity. The 6 sigma toolkit includes the entire set of quality tools. Some of them can be viewed in the Quality Tools section.
6 sigma as a methodology
Six Sigma is a process-oriented methodology aimed at improving labor. It allows you to improve all scopes of activity.
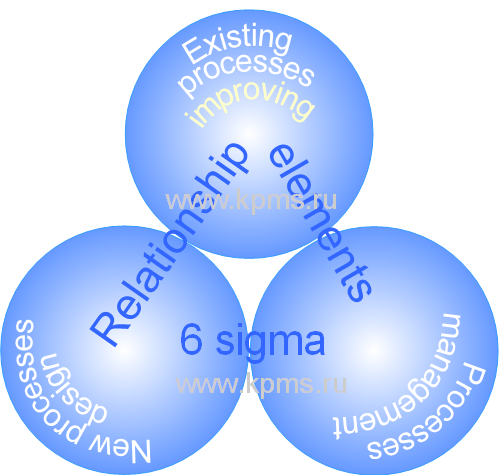
The 6 sigma methodology is based on three interrelated elements:
- existing processes improvement;
- new processes design;
- process management.
An incremental improvement approach is used to improve existing processes. The main focus is on reducing the level of defects. The purpose of the improvement is to eliminate disadvantages in the organization and execution of processes.
The improvement is carried out by applying five consecutive steps.
These steps are called the DMAIC method (the first letters from English words - Define, Measure, Analyze, Improve, Control):
- Define - The main problems of the process are identified, and the six Sigma project team is formed at this step. The team is given the necessary authority and resources to work. The area of team responsibility is established.
- Measure - Data about the execution of the process is collected at this stage. The team analyzes the collected data and makes preliminary assumptions about the causes of occurring deviations in the being improved process.
- Analyze - The team checks preliminary ideas about the causes of deviations in the processes, identifies all the causes of inconsistencies and suggests methods to eliminate the identified causes during this step.
- Improve – The actions are developed in order to improve the process and it is carried out the approbation these actions at this stage. The events are being implemented in the practice of the organization.
- Control - This step implies documenting and standardizing the improved process. The Six Sigma project team controls and monitors the execution of the process in order to check the effectiveness of the actions. Special attention is paid to checking the elimination of the nonconformance causes during monitoring.
It is applied an approach that aimed at anticipating customer expectations for newly created processes. The main attention is paid to the prevention of defects in processes.
Designing a new process (or redesigning an existing one) is also carried out in five steps.
The design (redesign) method in the 6 sigma concept is called the DMADV method (the first letters of the words - Define, Match, Analyze, Design, Verify):
- Define – The goals of the new process are defined, taking into account the requirements of customers at this step. A six sigma project team is formed to design (redesign) the process.
- Match - The team develops and defines a set of technical characteristics. It is possible to determine the achievement of the process goals based on these characteristics.
- Analyze - An analysis of the designed process characteristics is carried out and preliminary versions of the process are developed.
- Design – The detailed specifications of the new process are created and its implementation into the work of the organization is carried out during this step.
- Verify – The Six Sigma team performs a process check for achieving the set goals, taking into account the specified characteristics.
One of the important elements of the 6 sigma methodology is process management, because the organization very often in parallel improves existing processes and designs new ones. The managing of the continuously changing processes becomes quite a difficult task.
In general, the six sigma methodology in the part related the process management does not differ from the process management methodology.
The main elements of process management according to the 6 sigma methodology include:
- Identification of processes, key customer requirements and process owners;
- Indicators measurement that characterizing the achievement of customer requirements and key performance indicators of processes;
- The results analysis of the measurements and improvement of process control methods;
- The processes execution check that based on monitoring the "inputs" of processes, the progress of operations, and the "outputs" of processes and taking actions to eliminate problems or deviations from the established requirements.
6 sigma implementation
The implementation of the 6 sigma concept is based on the regular work of project teams. Teams are formed by management levels. As a rule, there are only three levels – the level of top management, the level of process management and the level of individual tasks. The teams include specialists with different "degrees of proficiency" in the six sigma concept.
There are seven degrees of ownership of this concept:
- General – It is the top management of the organization and business owners. The task of the top management is to create conditions for the implementation of the 6 sigma concept.
- Champion - As a rule, this is a representative of the top management of the organization. Its task is to identify the necessary projects to improve the processes, projects organization and monitoring of the progress of implementation.
- Master Black Belt - the task of this specialist is to develop the project concept of process improvement. He identifies the key characteristics of the processes, conducts training of black and green belts. The Master of the black belt is a "technologist" of the 6 sigma concept and an internal consultant.
- Black Belt - He leads the project team to improve an instance process. He can train project team members.
- Green Belt - He works under the guidance of a Black Belt. He analyzes and solves the tasks set, takes part in quality improvement projects.
- Yellow Belt - He solves private tasks in the project and is responsible for the implementation of small projects to improve processes.
- White Belt - He is responsible for solving individual, special tasks of the 6 sigma project.
The six sigma concept has become a well-known and popular brand at the present stage of development. The training of specialists at various levels of "ownership" of the 6 sigma methodology and their certification is facilitated by the promotion of this brand. It have been developed the certain training programs and requirements for the composition of knowledge, experience and qualifications for each of the above degrees according to the six sigma concept.